Comprehensive knowledge in the field of models and hydraulics
RUAG's aerodynamics department is synonymous for wind tunnel research, innovation, performance and efficient testing.
With decades of experience in wind tunnel testing, RUAG is a perfect partner for the development and manufacture of wind tunnel models. Using well-designed wind tunnel models, a high level of testing efficiency can be achieved, resulting in significant cost saving.
Our know-how - Your advantages
Contact
RUAG AG
Schiltwaldstrasse 1
6032 Emmen
Wind tunnel models
Modern development and manufacturing methods allow the highest surface accuracy. With the use of adequate materials such as metal, fiber composite and additive manufacturing, RUAG builds your subsonic or supersonic model, with or without integrated propulsion, in the best quality.
Hydraulic Engines
RUAG has a long history of design and operation of hydraulic systems in its wind tunnels. Hydraulics is used for actuators and to simulate the propulsion for powered wind tunnel models. In this context a number of technologies were developed such as finely controllable hydraulic power stations, balance crossings, and compact high-power, high-rpm hydraulic motors.
If handled and operated professionally, hydraulics is a very clean technology with a number of advantages over electric or pneumatic alternatives:
- Intrinsic heat removal, thus unlimited run times
- High power density
- No low temperatures due to gas expansion
- Inexpensive technology
Although developed for use in wind tunnels, these motors and associated systems are suitable for a wide range of applications, where high power densities, high speed and accurate control are required.
The motors are based on piston or in-house gear motor technology, readily scalable to the needed power levels and dimensions. The designs are unique compared to competitor designs with respect to power density (rpm and torque) and diverse options: hollow shaft, specific inlet/outlet topologies (lateral or coaxial), instrumentation, locking mechanism, selectable direction of rotation etc. The designs allow the simple setup of counter-rotating configurations, by two back-to-back mounted hydraulic motors.
Although developed to power wind tunnel models, these motors are suitable for other applications with similar requirements:
- Restricted volume (high power density)
- high rpm levels
- high torque levels
- stable temperatures
- coaxial drive system
- forces and moments to be measured
RUAG combines these motors with in-house developed rotating six component balances, telemetry and instrumented carbon model propellers which need to run within ±10 rpm of the customer required speed over the full rpm envelope and changing torque levels, e.g during pitch and yaw wind tunnel test runs.
Current Engine Portfolio
- MP10: 37.5 kW, 12‘000 rpm 82 x 110 x 153 mm (w x h x l)
- MG20: 75 kW, 10‘000 rpm, diameter: 140 mm (optional hollow shaft)
- MR07: 30‘000 rpm, 18Nm, diameter: 88 mm (optional hollow shaft)
- MR16: 12'000 rpm, 60Nm
The current portfolio is constantly growing driven by specific model requirements.
Nomenclature
M: Hydraulic motor
P: Piston type
G: Conventional gear motor
R: Gear motor, new generation
Number: nominal oil volume displaced per revolution
Download
Would you like to learn more about our services? Here, you can download various additional information.
SUITABLE TOPICS FOR FURTHER READING

Aerospace Wind Tunnel
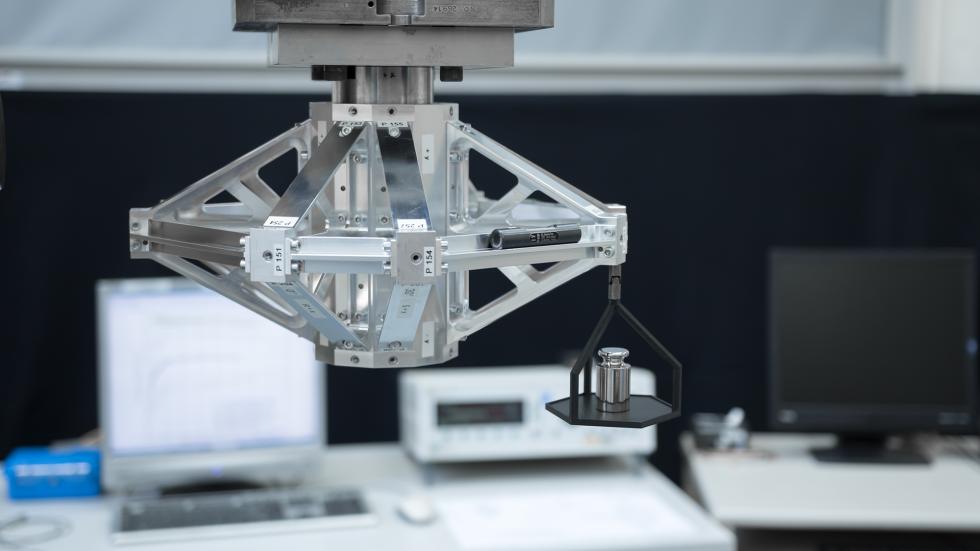
Balances & Instrumentation
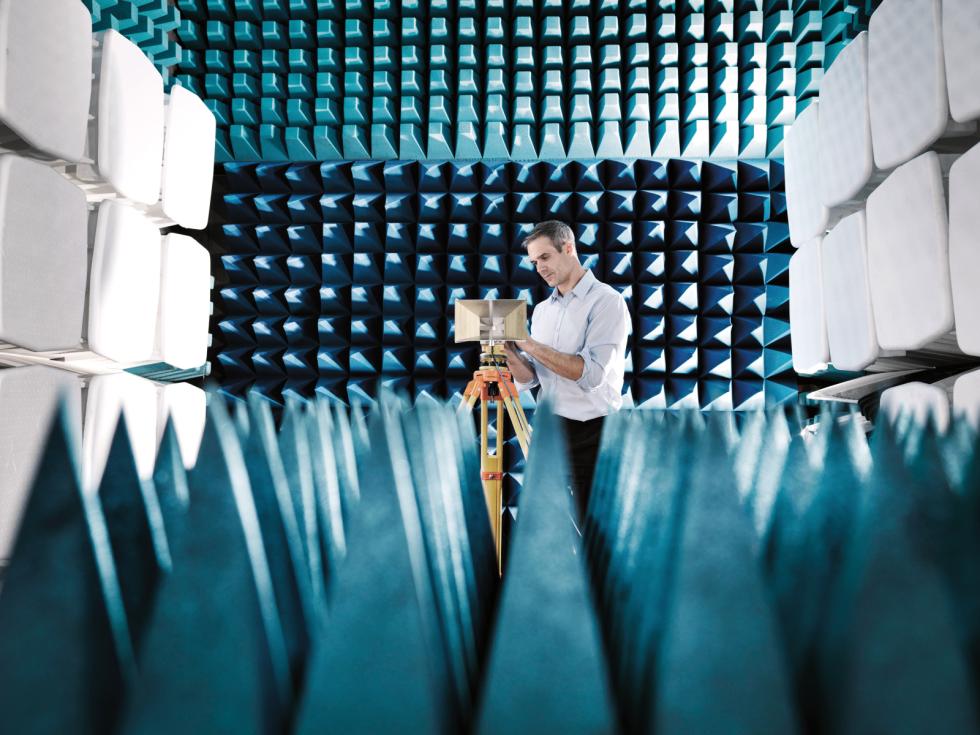