Material, process and testing
Materials testing is an indispensable instrument for quality assurance and quality control in many industrial sectors. Gas and oil supply, aircraft and bridge construction and the power plant operation would be impossible without the comprehensive control of materials through materials testing. Each safety-relevant component of a product must be tested in detail.
First-class quality is of central importance, providing you with a decisive competitive advantage. Extensive testing is required to ensure the quality of your products. Our comprehensive material testing procedures allow us to detect weak points promptly, ensuring improved quality of your products through detailed damage analyses.
OUR AREAS OF COMPETENCE
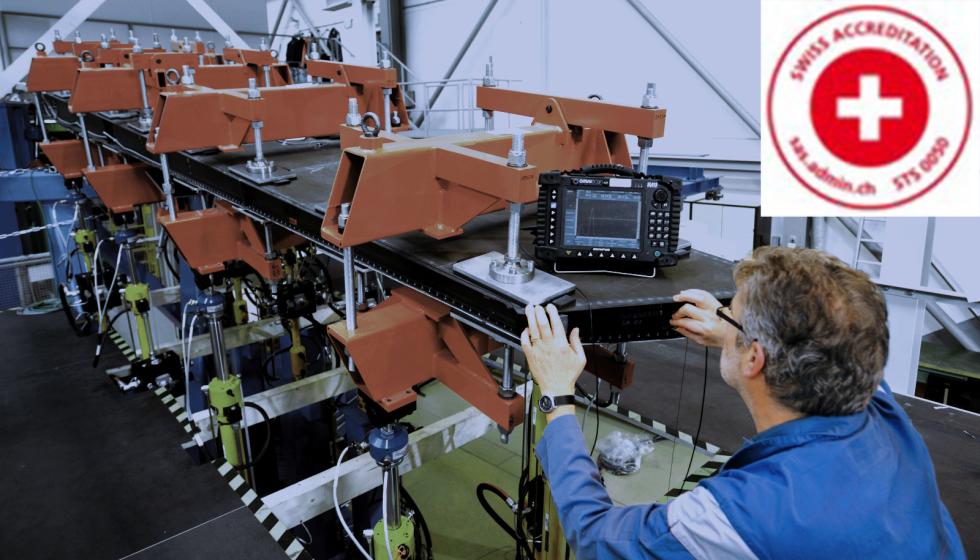
Structural testing
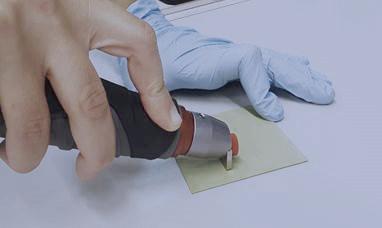
Process qualification
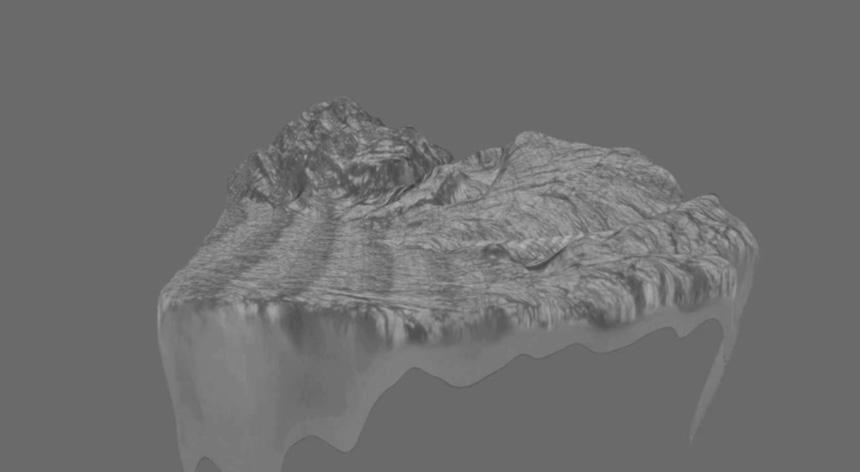
Failure analysis and material investigation
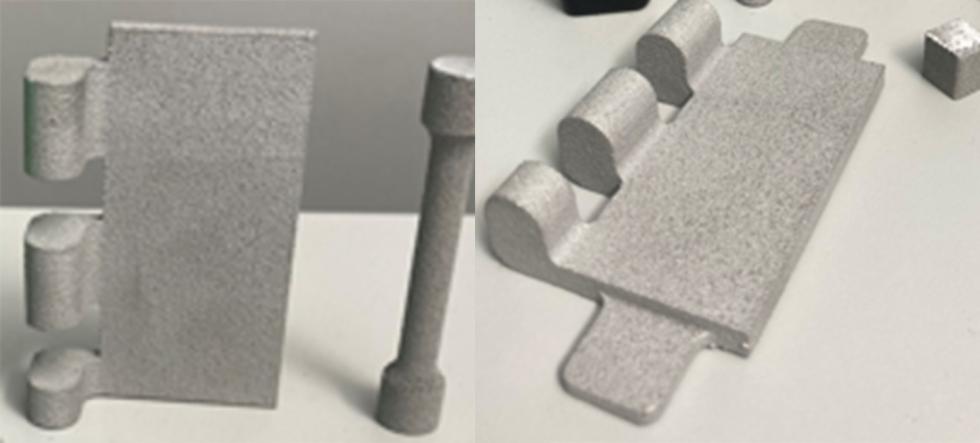
Additive manufacturing

Composite repair
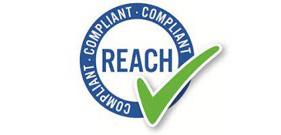
Obsolescence
Contact
RUAG AG
Seetalstrasse 175
6032 Emmen
Downloads
SUITABLE TOPICS FOR FURTHER READING
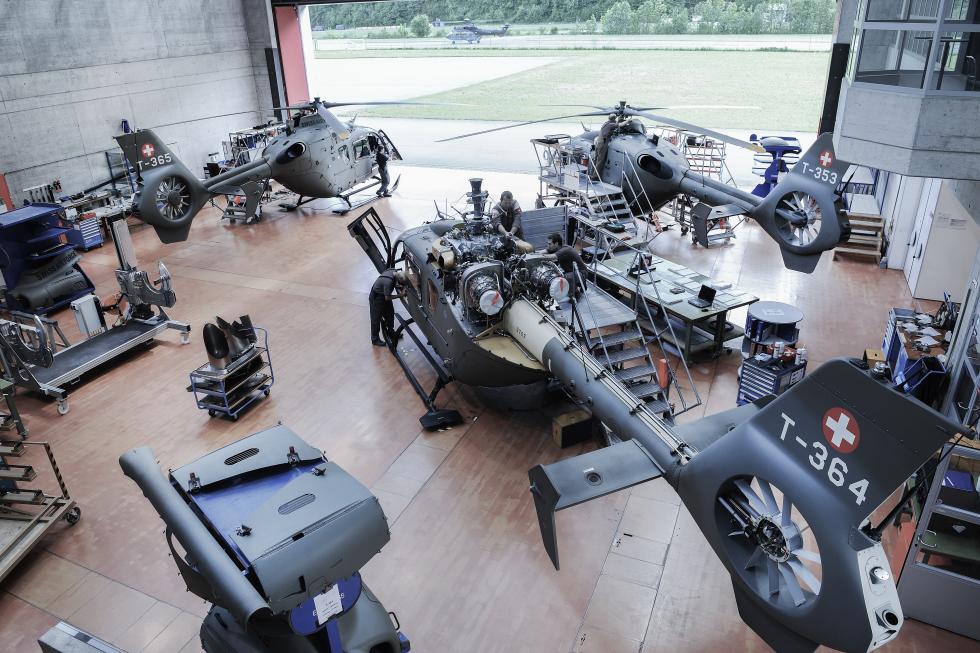
Your service provider for helicopters
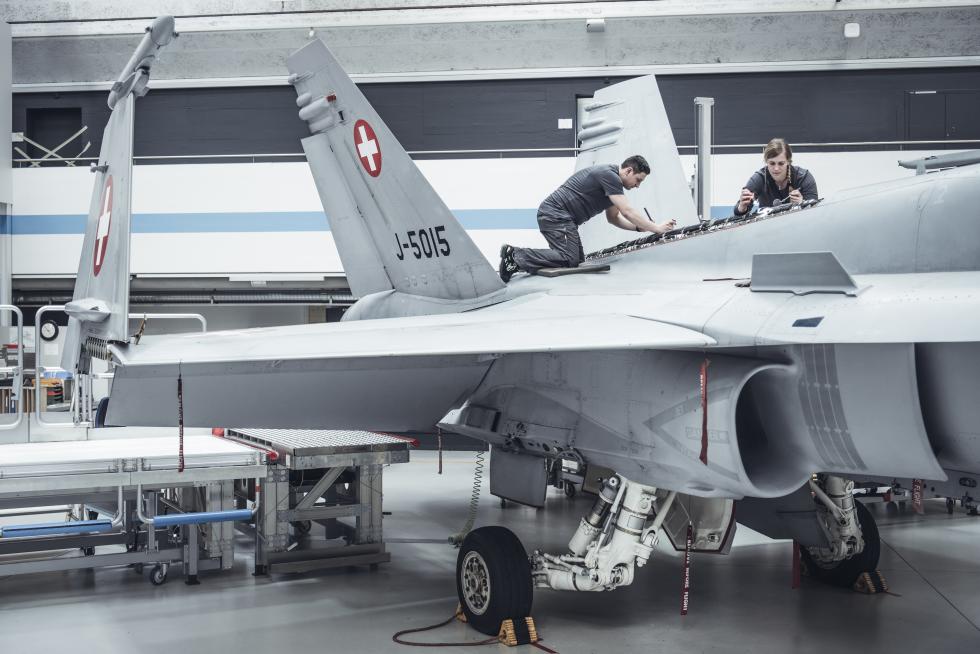
Life Cycle Management
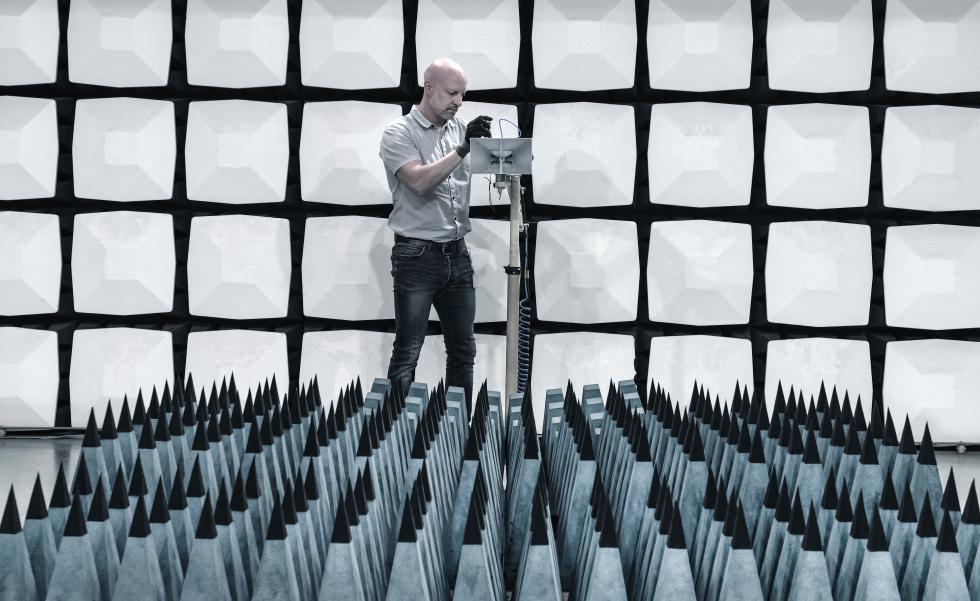